750ml Premium Vodka Bottles - Top Wholesale Options…
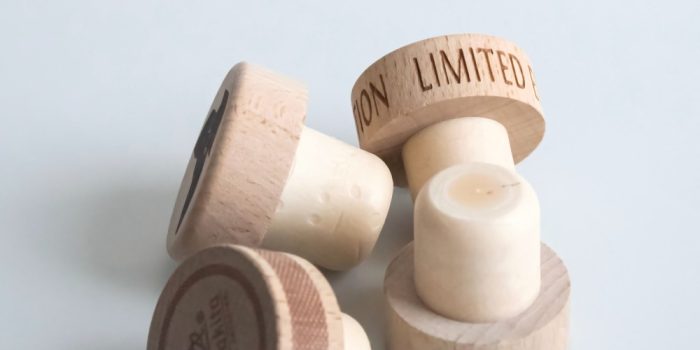
The Production Process of Cork Stoppers: From Raw Material to Finished Product
You must want to know how to do the cork stoppers, here’s the detailed production process of cork stoppers.
1. Raw Material Harvesting: Cork Oak Bark
- Tree Type: Cork comes from the cork oak tree (Quercus suber). These slow-growing trees with thick bark thrive in Mediterranean countries like Portugal (the largest producer), Spain, and Italy.
- Harvesting Process:
- First Harvest: The tree must be at least 25 years old before its bark can be stripped. This initial bark is coarse and used for flooring or insulation, not bottle stoppers.
- Later Harvests: After the first harvest, workers strip the bark every 9–12 years. Older trees produce thicker, higher-quality cork.
- Manual Stripping: Using short-handled axes, workers make vertical cuts along the trunk and carefully pry off large bark slabs. The inner layer (cambium) must remain intact to keep the tree alive.
2. Initial Processing of the Bark
A. Air-Drying
- Outdoor Seasoning: Freshly stripped bark is stacked outdoors for 6–12 months to:
- Allow natural moisture evaporation.
- Reduce tannins (compounds that can make wine taste bitter).
- Flatten the bark for easier handling.
- Indoor Drying: The bark is moved to warehouses with controlled humidity until its moisture content drops to around 15%.
B. Boiling and Sanitization
- Boiling: The bark is boiled in stainless steel tanks with purified water for 1–1.5 hours to:
- Soften the cork cells, improving elasticity.
- Kill insect eggs and bacteria.
- Remove dirt and impurities.
- Post-Boiling Drying: The bark is air-dried for 3–4 weeks in shaded, ventilated rooms to prevent cracking.
3. Grading and Cutting
- Quality Sorting: Workers inspect the bark for thickness, cracks, and color. The best sections become natural cork stoppers; lower-grade pieces are used for agglomerated corks or other products.
- Cutting into Strips: Rotating blades slice the bark into strips. For example, to make a 4 cm stopper, strips are cut to 4.5 cm to allow for polishing.
4. Punching the Stoppers
- Production Methods:
- Manual Punching: Skilled workers use hollow cylindrical knives to cut stoppers along the bark’s natural grain, avoiding cracks. This method is slow but precise.
- Machine Punching: Automated CNC machines cut hundreds of stoppers per minute, optimizing material usage.
- Types of Stoppers:
- Natural Cork: Made from a single piece of cork. Used for premium wines.
- Agglomerated Cork: Crushed cork granules bound with food-safe glue. Common in budget wines or sparkling drinks.
- 1+1 Cork: Features natural cork discs at both ends and a agglomerated middle layer. Balances cost and aesthetics.
5. Finishing and Quality Control
- Sanding: Belt sanders smooth the stoppers’ surfaces to remove splinters.
- Deep Cleaning:
- Soaked in hydrogen peroxide to sterilize.
- Treated with ozone to eliminate musty odors.
- Silicone Coating: A food-grade silicone spray is applied to ease insertion into bottles.
- Rigorous Testing:
- Compression Test: Machines compress stoppers to ensure they rebound to at least 95% of their original shape.
- Visual Inspection: Twenty workers sit along a conveyor belt, manually checking 8,000 stoppers per person daily for flaws like dark spots or cracks.
- TCA Screening: Random samples are ground and tested with gas chromatography for TCA (a mold-causing compound). Contaminated batches are destroyed.
6. Printing and Packaging
- Laser Engraving: High-end stoppers are laser-etched with winery logos and vintages (e.g., “2018 Château Lafite”). Budget stoppers use food-safe ink that resists fading.
- Vacuum Sealing: Stoppers are packed in plastic bags, vacuum-sealed, and filled with sulfur dioxide gas to prevent mold. A standard bag holds 1,000 stoppers.
7. Waste Recycling and Sustainability
- Byproduct Use:
- Cork dust is pressed into floor tiles (softer than wood).
- Fine powder is mixed with cement to create soundproof panels.
- Bark Residue for Energy: Unusable bark scraps are burned to heat water for the boiling tanks.
- Environmental Benefits:
- Cork oak forests shelter endangered species like the Iberian lynx.
- Each harvest boosts a tree’s CO₂ absorption by 3–5x. Portugal’s cork forests absorb CO₂ equivalent to 5 million cars’ annual emissions.
Advantages of Cork Stoppers
- Superior Seal: Expands when wet to block leaks but allows tiny oxygen exchange for wine aging.
- Renewable: A cork oak tree lives ~200 years and can be harvested 15–20 times.
- Fire-Resistant: Cork has a high ignition point and releases no toxic fumes when burned.
Challenges
- Rising Costs: Natural cork prices have tripled in 20 years, pushing budget wines to use plastic or screw caps.
- Competition: Synthetic alternatives are cheaper, but natural cork remains a status symbol for premium wines.
- Quality Risks: Though TCA contamination rates dropped from 10% to 0.5%, one tainted bottle can ruin a winery’s reputation.
Cork stopper production balances centuries-old practices with cutting-edge quality control, ensuring a product that is both eco-friendly and functionally superior. The process highlights the importance of sustainable forestry and innovation in maintaining cork’s dominance in the premium wine industry.