In the world of premium spirits, the bottle…
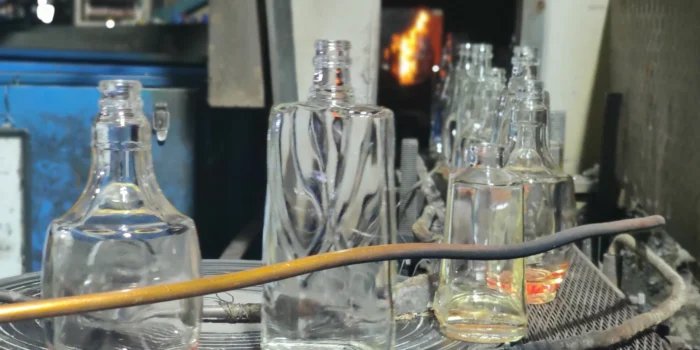
The Fascinating Journey of Glass Bottles Production
The Fascinating Journey of Glass Bottles Production
When we pick up a refreshing bottle of chilled soda or a sleek bottle of perfume, we rarely think about the intricate and fascinating process that brought that glass bottle into our hands. The Glass Bottles Production is a blend of art, science, and precise engineering. Let’s dive into this captivating journey!
Raw Materials: The Building Blocks
Glass Bottles Production begins with the gathering of raw materials. The primary ingredients are sand, soda ash, and limestone. These materials are carefully measured and mixed to create the glass batch. Here’s a quick look at each component:
- Sand (Silica): The main ingredient lending the glass its strength and transparency.
- Soda Ash (Sodium Carbonate): This reduces the melting temperature of the sand, making it more manageable.
- Limestone (Calcium Carbonate): Adds durability and helps to stabilize the glass.
Often, cullet (recycled glass) is also added to the mixture, which not only conserves raw materials but also reduces the energy required for the melting process.
Melting and Refining: From Solid to Liquid
Once the raw materials are ready, they are transported to the furnace. Furnaces in Glass Bottles Production are colossal, operating continuously at temperatures around 1500°C (2732°F).
- Loading: The mixture is loaded into the furnace where it starts to melt.
- Melting: The raw materials are liquefied to form molten glass. This process can take up to 24 hours and requires thorough mixing to ensure even consistency.
- Refining: Impurities and air bubbles are removed from the molten glass through refining, ensuring a high-quality glass free of defects.
Forming the Glass: Creating Shapes
As soon as the glass is molten and refined, it is ready to be shaped into bottles. The forming process is split into two main methods: blow and blow or press and blow.
Blow and Blow Method–Glass Bottles Production
- Initial Blow: The molten glass is gathered onto a blowpipe and shaped into a preliminary form (known as a parison) through an initial blowing process.
- Final Blow: The parison is then transferred to a final mold where compressed air is blown into it, forming the bottle’s final shape.
- Cooling: The formed bottles are removed from the mold and allowed to cool slightly before being transported to the next stage.
Annealing: Strengthening the Glass
The freshly formed bottles are still hot and fragile. To increase their strength and durability, they undergo a process called annealing.
- Annealing Lehr: The bottles are placed in a long tunnel-like oven where they gradually cool from around 600°C (1112°F) down to room temperature. This slow cooling process relieves internal stresses and minimizes the risk of breakage.
Quality Control: Ensuring Perfection
Quality control is vital in Glass Bottles Production. Companies employ stringent checks at various stages to detect and eliminate any defects.
- Visual Inspection: Trained professionals visually inspect bottles for any cracks, bubbles, or deformities.
- Automated Inspection: Advanced machinery uses cameras and lasers to check every bottle for consistency in thickness, shape, and volume.
- Stress Testing: Random samples undergo stress testing to ensure they meet safety and durability standards.
Decoration: Adding the Final Touch
Many Glass Bottles Production are further enhanced with decorations and brandings.
- Screen Printing: Ink is directly applied to the surface using a mesh screen, offering a permanent and vibrant design.
- Labeling: Paper or plastic labels are glued to the bottles, providing detailed product information.
- Etching and Embossing: For a more luxurious feel, some bottles undergo etching or embossing to add unique textures or designs.
Conclusion: A Bottle’s Journey to Your Hand
From raw materials to the finished product, the journey of a glass bottle is a testament to human ingenuity and precision. Each stage, from melting to molding, and from annealing to packaging, plays a crucial role in ensuring the bottles that reach us are not only functional but also aesthetically pleasing.
The next time you reach for a glass bottle, take a moment to appreciate the craftsmanship and technology that made it possible. The process behind that simple container is, indeed, a fascinating blend of science, art, and dedication.