In the world of premium spirits, the bottle…
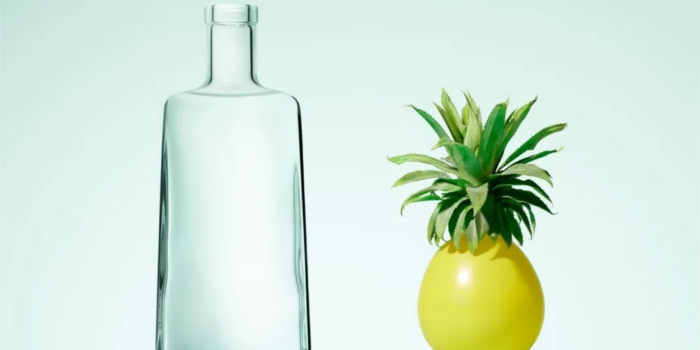
Hot Filling Spirits Production
Hot filling is an essential process in the production of alcoholic beverages.
Hot filling spirits production, particularly for those packaged in glass or plastic containers. This method involves filling and sealing the bottles with the product while it is still at a high temperature, typically immediately after pasteurization or sterilization. There are several reasons why hot filling is crucial for the alcohol industry, which can be broadly categorized into quality preservation, shelf life extension, and microbial control.
Quality Preservation
One of the primary reasons for hot filling in alcoholic beverages is to preserve the quality of the product. Alcoholic drinks are complex mixtures of various compounds that contribute to their flavor, aroma, and overall sensory experience. When a beverage is heated and then filled into a container, it minimizes the exposure to oxygen, which can cause oxidation and alter the taste profile. Oxidation can lead to off-flavors and a decrease in the desired characteristics of the beverage. Hot filling helps to maintain the integrity of the drink by reducing the risk of oxidation.
Moreover, the heat from the hot filling process can aid in the dissolution of certain ingredients that might be less soluble at lower temperatures. This ensures that the beverage is homogenous and consistent in taste and quality, from the first pour to the last drop.
Extended Shelf Life
The high temperatures used in hot filling are effective in sterilizing the inner surfaces of the container, which is particularly important for extending the shelf life of the product. By eliminating or reducing the number of microorganisms present in the container, the risk of spoilage is significantly decreased. This is crucial for non-alcoholic beverages, but it is also relevant for certain types of alcoholic drinks that may still be susceptible to spoilage over time.
The process of hot filling also creates a vacuum as the product cools down, which helps to draw the closure tighter against the container, creating a better seal. This vacuum seal is more effective at preventing the ingress of external contaminants, including oxygen and bacteria, which can compromise the quality and safety of the product.
Microbial Control
Microbial control is a critical aspect of food and beverage production, and hot filling plays a significant role in ensuring the safety of alcoholic drinks. The high temperatures used in the process are capable of killing most harmful bacteria, yeasts, and molds that could potentially spoil the product or pose a health risk to consumers.
By conducting the filling process at high temperatures, manufacturers can be confident that the final product will be free from harmful microorganisms. This is particularly important for beverages that are not intended to undergo a secondary fermentation or aging process in the bottle, as these could potentially create an environment conducive to microbial growth.
Packaging Material Adaptability
Hot filling requires the use of packaging materials that can withstand the high temperatures without losing their structural integrity or sealing properties. This often means using materials like heat-resistant PET bottles or glass bottles that are specifically designed for hot filling. These materials must be able to tolerate the thermal stress without deforming or losing their seal, ensuring that the product remains safe and secure within the package.
Production Efficiency
From a production standpoint, hot filling can increase efficiency by streamlining the bottling process. Since the containers do not need to be pre-sterilized, the overall production time is reduced, and the risk of contamination is minimized. This allows for a faster production rate, which can be particularly beneficial during periods of high demand.
Environmental Adaptability
Beverages that have undergone hot filling are better equipped to handle changes in environmental conditions, such as temperature fluctuations during storage and transportation. This is important for ensuring that the quality of the product remains consistent, regardless of the conditions it may be exposed to after leaving the production facility.
In conclusion, hot filling is a vital process in the production of alcoholic beverages that offers numerous benefits in terms of quality preservation, shelf life extension, microbial control, and overall production efficiency. By utilizing this technology, manufacturers can ensure that their products reach consumers in the best possible condition, maintaining the reputation and consumer trust that are essential for success in the competitive alcohol industry.
Hiking Glass is a renowned glass bottle manufacturer, committed to delivering durable, eco-friendly packaging solutions for various industries with a focus on innovation and customer satisfaction. Please contact us for more bottle details.